Glaze Transfer Application in the Refractory Industry
In the refractory industry, glaze transfer is essential for transporting viscous, abrasive, and reactive glazes through production line for continuous transferring. The efficiency of this process is critical, as it directly affects the end product's quality and durability, with inefficiencies potentially leading to defects, delays, and higher costs.
One of the leading refractory customers encountered challenges with traditional AODD pumps in this demanding application. These challenges were successfully addressed with the introduction of Cognito’s EODD pump. Let’s delve into the specifics of how this solution made a difference.
Customer Challenges
Higher Energy Consumption:
The process demanded continuous operation for 23-24 hours daily, resulting in substantial energy costs due to the need for a constant continuous supply of pneumatic air.
Lack of Safety Features:
The absence of leak detection mechanisms in AODD pumps led to undetected leakages from diaphragm ruptures, resulting in significant safety hazards and operational disruptions.
Elevated Maintenance Costs:
Frequent diaphragm ruptures due to the abrasive nature of the operating liquid, as well as the overall requirements of the pump assembly, resulted in significant maintenance costs.
Higher Downtime and Production Loss:
Frequent downtime and repairs impacted total expenses.
Process Details
The Right Solution
EODD pumps offer greater efficiency and power than traditional AODD pumps. Their electric operation and advanced safety features reduce energy use, quickly detect leaks and stop the pump, and ensure reliable performance. Additional safety features further lower maintenance costs and extend pump longevity in challenging conditions.
Unique Patented Diaphragm:
Engineered for durability, with optimized balance of diameter and stroke length for extended service life, increased longevity even in more abrasive fluids.
Seal-Less Design:
No seal failures/damages due to leaks. Leak detection sensors in place that eliminates the need for seals replacement, reducing maintenance requirements and minimizing potential failure points.
The Unique “Stopper Cage Design”:
Extends manifold life by protecting seats from abrasive fluids, preventing deflection, and increasing the lifespan of the manifold, head, and seats by 2 to 3 times.
Leak Detection Mechanism:
The Cognito team successfully convinced the customer to replace their 3” AODD pumps with 3” EODD pumps by showcasing the above benefits along with the ROI calculations. These features promised to cut maintenance needs, extend the lifespan of critical components by 2 to 3 times apart from the significant energy savings. These significant benefits made a strong case for the replacement.
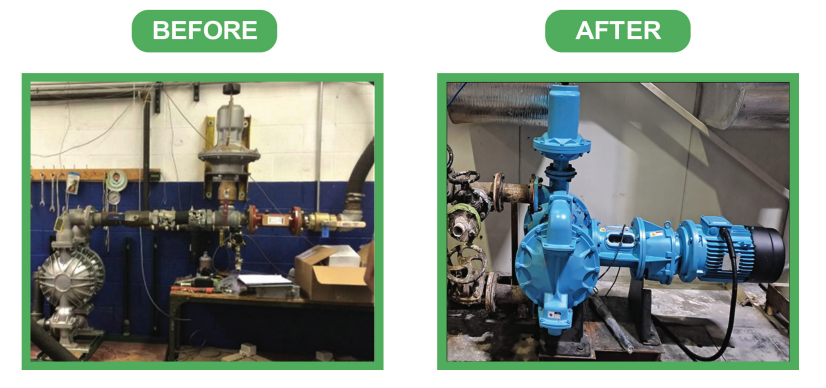
Customer Experience
The switch to Cognito’s EODD pumps has been transformative for the customer. They reported a substantial reduction in the energy cost, maintenance costs, and downtime.
Post-implementation, the customer observed significant improvements:
Phenomenal energy savings
Improved safety mechanism
Improved total cost of ownership
Reduced maintenance cost
Achieved ROI within 1 year
Energy Consumption Comparison: AODD Pumps vs. Cognito EODD Pump
Maintenance Comparison: AODD Pumps vs. Cognito EODD Pump
The customer expressed high satisfaction with the reliability and efficiency of their new system,
noting that the decision to replace the AODD pumps with EODD pumps has greatly improved their operational efficiency and overall cost-effectiveness. No diaphragm replacement or leakages seems from last one year from Cognito™ EODD pump. Installation date was 3rd of August 2023.
Download the Case Study
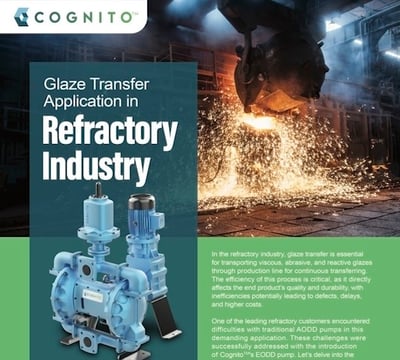
Want Your Organization To See Similar Results?
Contact an expert to learn more about our EODD pumps and how they can benefit your pumping operation.