Leading Producer of Metals Tackles Pumping Challenges in Their Filter Press Application
Filter Press Feeding
Highly abrasive and corrosive Alumina slurry/battery recycling paste is pumped from the slurry tank to the filter press machine for the separation of slurry into solid cake and liquid filtrate.
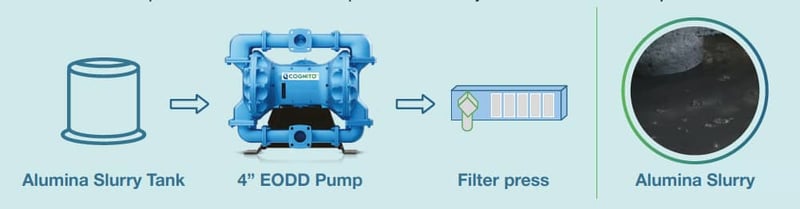
The Problem
As the applications dealt with corrosive, abrasive, and chemically aggressive fluids, safety and reliability were crucial.
The customer faced challenges with inefficient Peristaltic and centrifugal pumps due to the abrasive nature of the fluid, leading to downtime, safety risks, and operational inefficiencies.
These pumps struggled to handle back pressure efficiently during operation, leading to internal damages and subsequent leakages.
Ineffective pumping resulted in extended batch times and reduced overall throughput.
The customer required a reliable pumping solution that could manage aggressive fluids while ensuring a steady flow rate into the filter press chamber. The solution had to address back pressure issues and deliver a consistent flow rate to enhance better cake formation.
Challenges with Peristaltic Pumps (Hose Pumps)
- The hose had a short lifespan of 7-8 days, with spare parts costing 40% of the pump cost
- Excess pressure buildup leading to damage and safety concerns
- Increased downtime
- Decreased operational efficiency
- Costly maintenance
- Safety issues due to leakages
- Constant load on the motor leading to increased power usage and energy consumption
- Continuous monitoring of the hose to detect and prevent leakage
Challenges with Centrifugal Pumps
- Lack of reliability due to sudden & unexpected breakdown
- Longer batch time
- Limited pump lifespan of 2 months
- Higher Maintenance cost & downtime
- Frequent leakage from gland packing due to back pressure
- Safety concerns and unclean surroundings due to pressurized leaks
- Poor quality of cake formation
The Solution
The COGNITO™ team analysed the customer's needs and addressed the challenges related to managing highly abrasive fluids and back pressure issues.
Following a comprehensive evaluation, they proposed the 4” COGNITO™ Stainless Steel EODD pump with a Santoprene™ diaphragm, specially designed to meet the demanding fluid and process conditions. The system also included leak detection sensors and a VFD.
As a result, the client approved the replacement of few centrifugal pumps with COGNITO™ EODD pumps.
Incorporating the COGNITO™ EODD pump in their filter press application proved a significant transformation, addressing the earlier challenges - operational inefficiencies, downtime, safety concerns & recurring maintenance.
By integrating the VFD, the customer could adjust the flow rate/frequency, resulting in improved cake formation in a shorter duration.
The leak detection sensors helped to maintain safe working environment, minimizing the risk of hazardous spills.
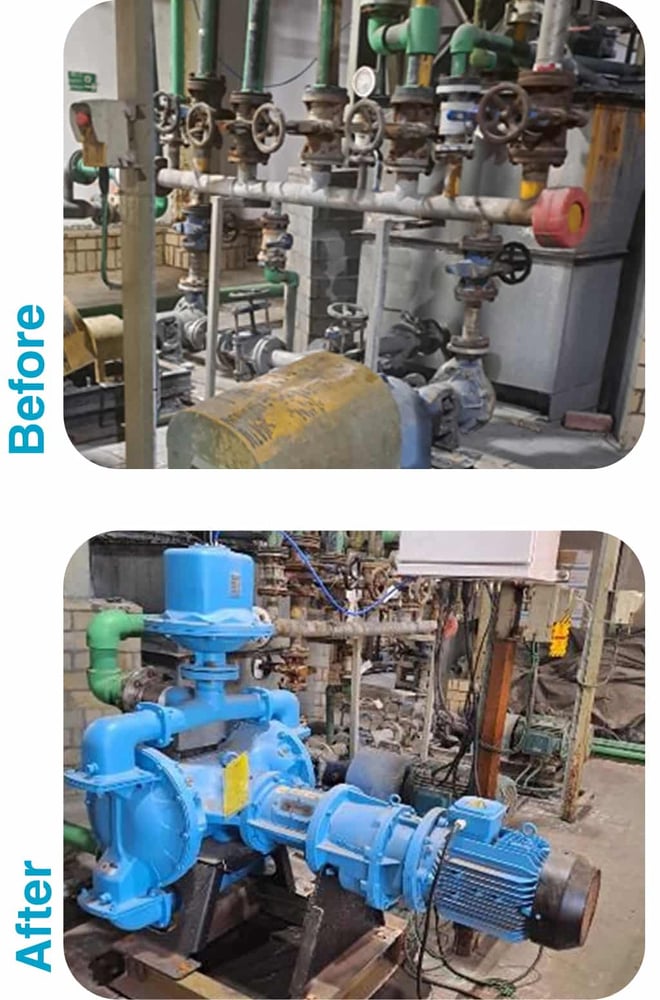
Download the Case Study
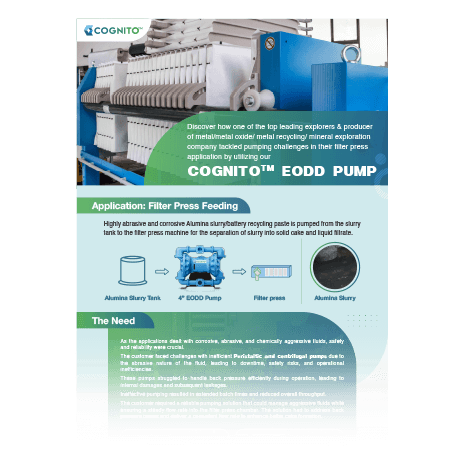
Want Your Organization To See Similar Results?
Contact an expert to learn more about our EODD pumps and how they can benefit your pumping operation.